Food Service
From commercial/industrial food service facilities to West Michigan school districts, Seaman’s Mechanical has the experience and knowledge to ensure your operations run smoothly. Our solutions are customized to meet your specific needs, including temperature regulation, process piping, ventilation, and more. You can count on our qualified service technicians to be on standby to handle scheduled maintenance and emergency situations.
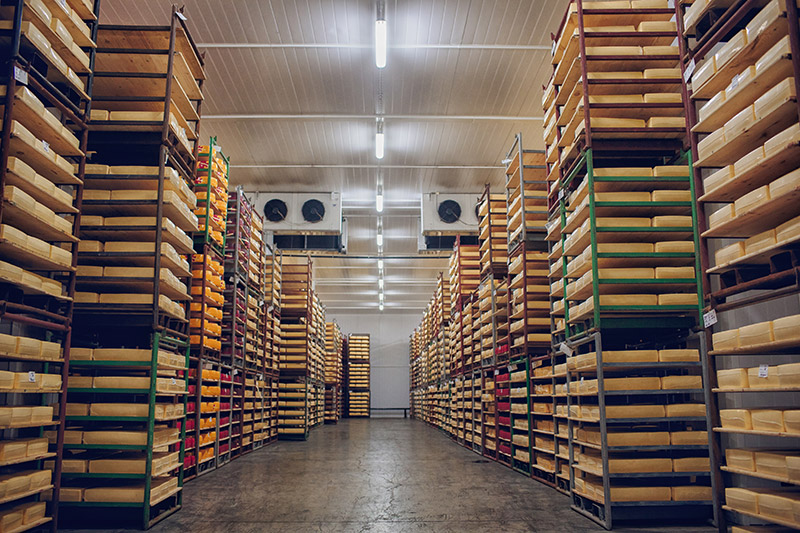
Systems Serviced
- Electrical & Plumbing
- Furnaces
- Ice Machines
- Kitchen Hoods
- Make-up Air Units
- Prep Tables
- Roof Top Units
- Reach-in Coolers & Freezers
- Drive-in Coolers & Freezers
- Walk-in Coolers & Freezers
Partial Client List
- Jenison/Hudsonville Public Schools
- Comstock Park Public Schools
- Ionia Public Schools
- Litehouse Foods
- Creme Curls Bakery
- Cedar Lake Foods
- Kent Quality Foods
- Ada Valley Meats
- Ferris Coffee & Nuts
Food Service Case Study
The situation: A local food manufacturing facility is expanding their building and adding additional product lines. High pressure steam is utilized for cooking which caused elevated temperatures in the factory. Being a food manufacturing facility regularly cleaning of equipment and floors with hot water is required, causing a very wet and high humidity environment. There was no air conditioning in the factory, so summer conditions were very uncomfortable with indoor temperatures topping 100° F at times. They had higher than normal employee turnover, not to mention the constant battle with mold growth, and slippery floors.
Seaman’s was called: With the upcoming expansion, the client wanted to know what it would take to air condition the factory. Seaman's sat down with the client to determine if simply adding air conditioning would address all their issues. It was determined the root cause of the problems was not the space temperature, but rather the wet conditions and high humidity. Mechanically removing the moisture would lower the humidity, slow the mold growth, keep the floors drier, and lower the temperature in the factory to a tolerable level, which ultimately would lessen employee turnover.
Seaman's solution: It was determined that packaged roof mounted Direct Expansion Dehumidification units with Natural Gas reheat would be the most practical and cost-effective solution to the problem. Building automation controls were added to operate the equipment with computer access provided to the client for set point adjustments and monitoring of the systems. The system was designed to control humidity first, with cooling as a secondary function. The humidity went from 75% down to a constant 55%. Floors and equipment dried much faster after wash down, mold growth slowed substantially, and indoor temperatures in the summer were lowered to a tolerable 78° F. The employees were much happier, which led to high productivity and less turnover.